Students Teach Army About Rapid Prototyping
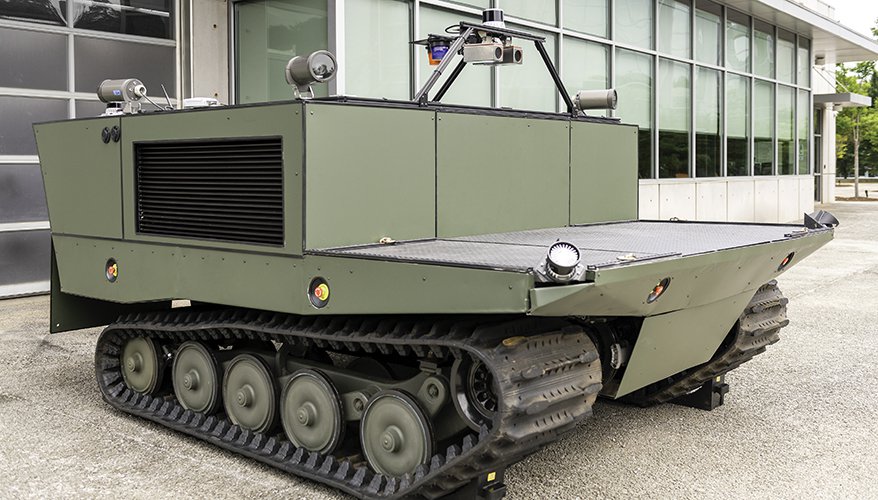
Clemson University photo
NOVI, Michigan — Whether it is through new offices, contracting methods or digital prototyping, the Army is trying to speed up the development and deployment of new vehicle technologies. A team of university students just might have a thing or two to teach the service.
Master’s degree students in Clemson University’s automotive engineering department took a set of requirements and about $1.5 million from the Army Combat Capabilities Development Command’s Ground Vehicle Systems Center — or GVSC — and 18 months later unveiled Deep Orange 13, a fully autonomous, high-speed, off-road vehicle.
The 3,500-kilogram, non-combat vehicle — a green, boxy, tracked platform about the size of a sport utility vehicle festooned with cameras and sensors — debuted recently at the Ground Vehicle Systems Engineering and Technology Symposium organized by the Michigan chapter of the National Defense Industrial Association.
“When we first started the project, they gave us a lot of requirements that they were really looking for as far as gradeability and water fording depth,” said Christian Johnson, student project manager for Deep Orange 13. The vehicle was designed to address two mission scenarios, he added.
The first scenario the Army provided was a post-snowstorm operation where the vehicle has to traverse off-road terrain to deliver 600 kilograms of supplies and supplemental electricity to civilians in need. The second scenario was an urban reconnaissance mission where the vehicle has to navigate flood waters, identify and geotag victims within a five-kilometer radius and deliver relief supplies in a 48-hour period without refueling.
The students started their design with no preconceptions about form, drive system or other technologies, said Anirudh Sundar, Clemson graduate student and chief vehicle engineer.
“We tried to quantify all this using metrics to sort of justify every decision that is taken on the vehicle, whether it is the choice of tracks versus wheels or whether it is a choice of the powertrain architecture, or whether it is the choice of the kind of cooling system you use,” he said.
“Every aspect of this vehicle goes through a systems engineering approach, where we arrive at a decision matrix of all the possible alternatives that can be used and then weigh that against the value it adds to the project,” he added.
From there, the students began making decisions and mapping out the basic configuration using computer-aided design. It began to take shape — the vehicle would use tracks instead of wheels and would be a diesel-electric hybrid, he said.
The team completed 90 percent of the design digitally, creating complex models to predict the behavior of systems under different scenarios. Once students completed the digital prototype, they set up test benches to evaluate and validate the functionality of the individual components, he said.
The team chose, like previous Deep Orange projects, to use only commercial-off-the-shelf products for all the components — motors, drivetrain, lithium-ion battery, cameras, sensors — and custom build the frame and wiring to connect it all. That allowed the students to keep costs down and meet the tight production deadline, he said.
“We have to finish this in 18 months,” he said. “So, timeline, cost are all practical factors that really factor into the selection of components of this vehicle.”
Once the components were validated and assembled into the physical prototype using the GVSC-provided autonomy stack, the question was whether everything would play well together.
“We first ran this vehicle in July [2022],” he said. “We came up with a lot of faults because you had so many systems interacting, some overriding the others, but then we came to a point where the whole vehicle was running smoothly.”
The autonomy worked, the vehicle ran solely on electricity and the internal combustion engine generated power that could charge the battery and power external systems, he said.
As they increased the complexity of the testing, they encountered a mechanical failure and then a communications fault, he said.
Still, by the time of the August public debut of the vehicle, they had completed 95 percent of the basic goals for the vehicle, he said. For example, the specification required the vehicle to turn 360 degrees in place within 12 seconds. The prototype did it in eight.
“We know that we can even shorten that because the potential of the motor and the drive system we have can give us instant torque,” he said. Students will continue testing and refining the vehicle over the next year, he added.
While the requirement was to build a one-off research vehicle, “unintentionally, what we’ve ensured is that every component of this vehicle is a purchasable off-the-shelf component,” he said. And the frame and wiring harness the students designed are documented in CAD so the whole vehicle can be reproduced.
However, scaling and fielding a version of Deep Orange 13 isn’t the objective of the program. The project is part of a larger contract between GVSC and Clemson to advance digital modeling of ground vehicles.
GVSC has been partnering with Clemson through the Automotive Research Center, a consortium of universities working on modeling and simulation of ground systems for the Army that was founded in 1994 at the University of Michigan.
In 2020, GVSC entered into a five-year agreement worth up to $100 million with Clemson’s Virtual Prototyping of Ground Systems Research Center, or VIPR-GS. Under that agreement, Clemson and GVSC are engaged in a range of projects around autonomy for off-road vehicles, propulsion systems, hybrid and electric power and manned-unmanned teaming.
Previously, auto manufacturers like Ford or Honda funded Deep Orange projects to produce autonomous vehicle prototypes, like last year’s autonomous race car.
With the funding agreement in place, GVSC saw an opportunity to sponsor a Deep Orange project that could help advance the Army’s autonomous vehicle development efforts, said David Gorsich, chief scientist for Army ground vehicle systems.
“So, we made [the requirements] very similar to the Robotic Combat Vehicle-Light Program,” he said on the sidelines of the symposium. The RCV-L program — part of the Next-Generation Combat Vehicle Program — is still in the pre-competition phase and is identifying capability gaps, ones that perhaps the students can solve, he added.
“We said, ‘See what you can do.’ So, it’s learning the prototyping process and then seeing if they can come up with some innovative solutions to problems that we have in capabilities,” he added.
“What they learn will come back to us and our industry members,” working on the RCV program, he said.
And while the hope is that the Deep Orange 13 project might find solutions to RCV capability gaps, that is a secondary objective. The project is more about advancing modeling and simulation technology tools by using those tools to design an RCV-L platform virtually and then build a physical prototype, he said.
“When you build the prototype, that informs you on what you can do well from your virtual prototyping perspective and what didn’t you do well,” he said.
“Once the prototype is built and they start testing it, they find out OK, there’s problems with the autonomy stack on this platform. There are other issues we couldn’t predict that came up,” he said. “All those lessons learned help go back and teach us about — not just how to build a prototype vehicle like RCV and those challenges — but the virtual prototyping tools themselves, how well they could do.”
It is essentially a digital-to-physical-to-digital feedback loop. For example, VIPR-GS will “retrofit the tracks with sensors and create a virtual twin where this vehicle will be used as a test-bench for their research,” said Matthias Schmid, assistant professor in Clemson’s department of automotive engineering.
“And it is a little bit contradictory because we are here with this as a physical prototype for a center, which is called ‘virtual prototyping center,’” he said. “But physical prototype building is still an essential part of virtual prototyping and digital twinning, just in a smart way that you can validate your models, you can verify what you’ve done and then streamline design processes in the future.”
“It is just not possible to do anymore applied, conventional, traditional design methods,” said Zoran Filipi, VIPR-GS founding director. Technology is advancing too quickly, requirements are increasingly complex and spending four to five years developing a prototype is too long, hence the need to embrace virtual design, he added.
“The ground vehicle world is now marching in that direction,” he said. “And GVSC, despite the fact that they are a really formidable organization … they discovered they simply don’t have internally enough of a capacity to address this big, big challenge.”
“The Army is interested in, as weird as it sounds, rapid failure,” said Schmid. “Rapid failure means we cannot afford anymore to work on something for 10 to 15 years and then figure out that it doesn’t work.”
Hence, GVSC is leveraging the Automotive Research Center and the capacity of universities like Clemson to advance virtual prototyping tools and approaches, Gorsich said.
“But we also had to make sure that since we’re working with a group of students … we didn’t get into any kind of information that would be restricted,” he said. That meant that nothing controlled or sensitive like the robotic technology kernel, which is at the core of Army ground vehicle autonomy software, he added.
“In an academic context, it is somewhat unique to have a full-scale tracked vehicle of this size and scope available to researchers,” said Chris Paredis, director of the Deep Orange Program.
“Most of the vehicles of this nature, truly military vehicles, they are classified and accessing data about these vehicles is not something that is typically possible,” he added. “So, having now a research prototype that can be used to collect data to explore limits of algorithms and further develop new algorithms is a great asset for the center.”
The program is also designed to serve an even larger, longer-term purpose, said Gorsich and Clemson faculty members.
“The programmatic goal of Deep Orange is talent — educating students, feeding them to defense companies, in this case to the Army,” said Schmid.
Students are interacting with government engineers and scientists and industry partners who are involved in the program.
“How many people have actually had a chance to actually build a prototype vehicle?” said Gorsich. “Having young engineers and scientists like that is just really important for workforce development.”
GVSC tracks the students at Clemson and the other university partners to see if they take industry or government jobs. Either way, it is a win, Gorsich said.
“If they come to our industry partner and give them that capability and experience … that’s great. It comes right back to us from what our industry partners do for us.”
Topics: Army News, Robotics and Autonomous Systems
"about" - Google News
September 24, 2022 at 02:45AM
https://ift.tt/9fQYrE4
Students Teach Army About Rapid Prototyping - National Defense Magazine
"about" - Google News
https://ift.tt/OlgopCF
Bagikan Berita Ini
0 Response to "Students Teach Army About Rapid Prototyping - National Defense Magazine"
Post a Comment